Visita a GIVI Italia
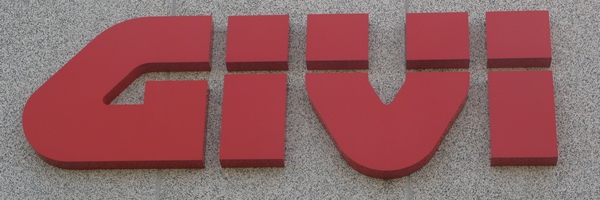
En un principio, la dedicación de Giuseppe se centraba en la producción de accesorios para motores. Más tarde y tras ver las necesidades de los motoristas por transportar sus pertenencias en la moto, se dedicó a trabajar en el diseño y la producción de portaequipajes, maletas y baúles con sus respectivos anclajes; para seguir más adelante trabajando en el área de seguridad del piloto con la fabricación de cascos y otros accesorios varios. Todo ello con tecnología innovadora y el marchamo de -Diseño italiano-. La mayoría de los trabajadores de Givi son usuarios o aficionados a la moto, algo esencial para comprender las necesidades de los motoristas. Además, trabajan aplicando los ocho principios de la filosofía GIVI: Armonía, Entusiasmo, Consideración, Inteligencia, Innovación, Gratitud, Tolerancia y Felicidad.Al contrario de otras empresas recelosas de enseñar sus entrañas, Givi nos abrió las puertas de su entramado empresarial para mostrarnos cómo trabajan y quién está detrás de los productos Givi que utilizamos a diario.
La central de Givi está situada al norte de Italia, concretamente en Brescia. En esta sede se aglutinan todos los departamentos de I+D, dirección y administración, mientras que en un radio de 20 Kilómetros se encuentran otras cinco grandes naves que completan la compañía en Italia y engloban las áreas de producción, elaboración de moldes, inyección, montaje, pintura, almacenamiento y distribución. Estos últimos cuentan con un sistema avanzado de gestión logística informatizada que verifica todos los movimientos paso a paso. También es necesario añadir la presencia directa de Givi en varios países del mundo para ofrecer una respuesta inmediata a las demandas, y cumplir así con su objetivo de -Calidad total-.
El proceso:
Todo comienza en la oficina de I+D, cuando se reúne el equipo de ingenieros, diseñadores, product managers y técnicos; y empiezan a dar ideas de los posibles productos a realizar, ya sean nuevos o -restylings- de los ya existentes, gracias a las sugerencias que les transmiten todos sus dealers repartidos por el mundo.
Por medio de las maletas, intentan adaptar los modelos ya existentes a los nuevos tipos de motocicletas, pero siempre buscando dar un paso más allá y crear cosas nuevas. Con las ideas alcanzadas en la reunión, el diseñador comienza a trabajar con el ordenador, siguiendo los parámetros acordados hasta que realiza un boceto al gusto de todos. A partir de este momento y una vez filtrados todos los parámetros de la muestra, se envían al arquitecto-diseñador, quien se encarga de crear el producto aún de manera virtual con un sofisticado software llamado ALIAS, similar al utilizado por FIAT. De aquí se moldea una muestra de madera en escala 1:1 y se hacen pruebas, que en el caso de las maletas se realizan sobre la propia moto para analizar diferentes aspectos como la aerodinámica, la estética, las sensaciones, etc. Se van resolviendo entonces las posibles pegas que vayan surgiendo y, una vez que el prototipo está listo, se pasa por un escáner que toma todas las medidas y las transfiere a un ordenador. Éste recrea el escaneo en un modelo en 3D que aporta los datos matemáticos necesarios para permitir la elaboración de los moldes de cada una de las piezas que componen el producto, para la inyección del plástico y posterior fabricación de las piezas. Una de las tareas más complejas y delicadas consiste en la elaboración de las tapas y fondos de los baúles, que requieren complejos y caros estudios de movimientos internos, líneas de refrigeración, extractores, torsiones, etc.
En principio, parece un proceso sencillo, pero cada uno de estos pasos lleva un gran trabajo de investigación detrás, un esfuerzo que no se ve cuando compramos los productos de Givi, y que os queremos mostrar visualmente en este reportaje. Dentro del departamento de I+D, existe también un laboratorio en el que se testan todos los productos para certificar su calidad y, en el caso de los cascos, donde se realizan los test propios para la homologación europea.
Producción del molde
Con el diseño en 3D se procede a la creación del molde en acero o aluminio que, en función de la complejidad, puede alcanzar un coste de 70.000 – y supone el trabajo de cuatro personas durante dos meses. Givi dispone de máquinas de precisión para fabricar los moldes, pues no quieren hacerlos en China y abaratar la producción de los mismos debido a que la experiencia les enseñó que al final resultan más caros. En China elaboraban dos moldes por un precio más económico, uno para el mercado de Givi y otro para uno paralelo. De esta forma, cuando querían lanzar la nueva gama, ya estaba en venta una paralela con marca china.
El diseño en 3D de los moldes es enviado a estaciones que comienzan el proceso de elaboración. En primer lugar, de manera virtual, utilizando un software que permitirá a los operadores de las fresas elegir las herramientas más adecuadas para cada fase de la elaboración. Posteriormente, se efectúa el trabajo, esta vez de manera real sobre el metal.
El software CAM conduce la trayectoria de la herramienta. Es un archivo que contiene una secuencia de coordenadas en lenguaje de máquina que se ejecuta numéricamente y es recibida por la fresa para efectuar el proceso de modelación y creación del molde. Esta fresa es capaz de mover su herramienta en el proceso de modelaje, a través de un total de 5 ejes, mientras que una fresa normal lo efectúa en los 3 ejes clásicos, con movimientos en los ejes X, Y y Z. El hecho de trabajar con un mayor número de ejes permite obtener unos resultados que de otra manera no serían posibles.
La máquina dispone de un rango máximo de trabajo de 2m, lo que puede permitir que se realice una producción de un mayor número de moldes automáticamente.
La velocidad máxima de trabajo de la herramienta durante el proceso de mecanizado es de 120m/min. Para efectuar esta alta velocidad y su elevada aceleración (que también llega a 1,2 g), la máquina está equipada con motores lineales.
También, hay otras fresas que pueden realizar el procesamiento de los bloques de un tamaño mayor.
De aquí se pasa a la zona de -electro erosión-, donde una máquina efectúa los cortes complejos y precisos, incluso con conicidad variable, siguiendo un archivo de programa con el diseño deseado. Esta -electro erosión- se lleva a cabo mediante inmersión a través de un electrodo, y está especialmente pensada para elaborar las formas deseadas en el molde, en aquellas partes que son imposibles de conseguir con el proceso de la fresa. En cuanto a la -electro erosión-, puede definirse brevemente como un proceso de rebaje del metal a través de un electrodo de polo opuesto que activa las chispas por medio de un campo magnético.
En el molde abierto se observa la complejidad de la mecánica, el movimiento, el proyecto, la realización, la precisión, las tolerancias de la elaboración, la buena ejecución, etc. Todas estas características se concentran para conseguir una efectiva utilización del molde en el proceso de prensado. Es decir, un modelaje real y propio.
De hecho, el proceso de moldeado es capaz de demostrar en la práctica, si el molde es diseñado e implementado de manera eficiente (a través de los datos del proceso), la posibilidad de realizar las piezas de fundición automáticamente, etc.
Durante el proceso, el molde está sujeto a una considerable tensión dinámica y a unas condiciones de temperatura muy diversas en las diferentes fases de la elaboración. El intenso calor producido por el material fundido hace dilatar el acero y se corre el riesgo de dañar algunas partes del molde.
Estación de inyección plástica, Technopolymero.
Mediante la prensa japonesa TOYO de funcionamiento eléctrico, se ejerce una presión de 680 toneladas por medio de motores eléctricos en lugar del método tradicional por presión hidráulica. Esta característica mejora la precisión de ajuste del recorrido y el progreso de las placas. Además, la utilización de una máquina eléctrica supone un paso adelante en el discurso por el ahorro de energía y el impacto ambiental.
GIVI demuestra así ser muy sensible en este aspecto, ya que cinco prensas de un total de trece son eléctricas. Cada prensa tiene su propia estación con robot automatizado para la extracción de las piezas y todas se colocan en las bandas transportadoras para converger finalmente en el área de palatización, con el objeto de ser embaladas como semielaboradas.
El material llega a las prensas por medio de un sistema centralizado que puede abastecer a cualquiera de ellas. Antes de ser utilizados, algunos de estos materiales deben pasar un ciclo de secado o de deshumidificación. Se usan muchos tipos de materiales plásticos de los mejores fabricantes de todo el mundo, que son más caros, pero garantizan la calidad del producto en el proceso de mecanizado.
La prensa eléctrica NEGRI BOSSI 550 se utiliza para estampar baulotes usando como manipulador un robot antropomorfo (que simula la forma humana). El robot es programable y se puede utilizar también en otros procesos.
El material bajo la forma de tecnopolímero en grano llega calentado por la fricción de un gran torno situado en el interior de un cilindro y sujeto a esta temperatura por una serie de resistencias controladas por un termostato.
El material llega a la temperatura de fusión y se inyecta a alta presión, a un promedio de 2000 bares en la cavidad del molde para llenar y completar todas la partes y detalles con la misma presión y proporcionando de esta forma la misma calidad en toda la plastificación.
Que una prensa sea de 550 toneladas significa que su fuerza máxima de presión de una parte contra la otra es de 550.000kg. Es necesario extremar y equilibrar esta fuerza y la inyección de alta presión del material fundido, ya que de otra manera se podría abrir el molde, causando defectos en el proceso.
Las prensas son controladas en todo momento por un servidor que proporciona unos programas con los datos necesarios para la producción, el número de piezas, los lotes, las características, etc.
Además, el servidor registra toda la actividad de las prensas y es capaz de proporcionar datos en tiempo real a los empleados que necesitan consultarlos, la producción llevada a cabo, las estadísticas, las proyecciones, la cantidad de los posibles residuos, el consumo de energía y mucho más.
Existen prensas de menores tamaños para la producción de pequeñas piezas, mucho más rápidas y precisas.
En la zona de las prensas de inyección se efectúa el primer control visual de calidad, para, a continuación, seguir con las pruebas adicionales del laboratorio con objeto de verificar tanto las especificaciones técnicas del producto como las mecánicas de la pieza producida.
Tras cada producción, se limpian los moldes y se almacenan para posteriores ocasiones. Un molde se llega a usar más de 300 mil veces.
Proceso de pintura.
Las piezas de plástico que necesitan pintura son enviadas a las cabinas de pintura para seguir un proceso automático del mismo, con el control de calidad propio de cada fase.
Las piezas son montadas en una cadena de pintura para su preparación previa. Primero, se eliminan los restos de silicona que pueda contener el material, luego pasa a un pulido de la pieza con producto antiestático para entrar en la primera cabina de pintura, donde un robot imprima toda la pieza por igual. Tras un secado de 15 minutos, entra en la cabina de pintura opaca y seca unos veinte minutos antes de pasar por la última cabina, donde se le aplica la laca y se pasa a un horno a 70º durante 40 minutos. Todas las piezas son sometidas a un control de calidad con revisión y pulido antes de empaquetarlas para su almacenaje y posterior montaje.
Cadena de montaje.
En función de las necesidades, se van ensamblando las unidades requeridas en una cadena de montaje manual, en la que se controla todo el proceso y se certifica la calidad del producto. Una vez montado el producto, se empaqueta y se almacena en las naves informatizadas, para ser remitido a los mercados.
Dentro de los almacenes se encuentra el departamento de logística, que es el encargado de preparar y empaquetar los pedidos que reciben. El proceso de control de stock está completamente informatizado y cada pedido lleva un código que asocia el número de piezas a incluir. Cuando el operario se equivoca, este control salta y no deja seguir con el pedido hasta que no subsana el error. Una vez metido el producto en la caja, se inserta el albarán y pasa a ser precintado automáticamente, quedando listo para su envío a cualquier parte del mundo.
Logística.
Dentro de los almacenes se encuentra el departamento de logística, que es el encargado de preparar y empaquetar los pedidos que reciben. El proceso de control de stock está completamente informatizado y cada pedido lleva un código que asocia el número de piezas a incluir. Cuando el operario se equivoca, este control salta y no deja seguir con el pedido hasta que no subsana el error. Una vez metido el producto en la caja, se inserta el albarán y pasa a ser precintado automáticamente, quedando listo para su envío a cualquier parte del mundo.
GIVI, una gran empresa sensibilizada con el medio ambiente y volcada en hacer más agradable a los motoristas los desplazamientos en moto.